Sin duda, la gestión de residuos de cualquier actividad ganadera, y más en concreto la gestión de residuos de incubación, siempre ha originado una situación de crisis y de aviso de colapso, lo que ha forzado que el propio Sector de Incubación haya trabajado de manera muy eficiente encontrando procesos industriales, que han permitido elevar gran parte de esos residuos a la categoría de Subproductos, con la valorización consiguiente. Esto es, hemos transformado un coste y un problema, en un ingreso y una oportunidad de negocio, y así lo hemos hecho en IBERTEC en España, en una planta de incubación con una producción anual de 15 millones de pollitas LOHMANN.
CUANTIFICACIÓN DE LA GENERACIÓN DE RESIDUOS .
En primer lugar, vamos a proceder a realizar un repaso sobre las magnitudes de residuos que se generan en una planta de incubación. Cuando cargamos en nuestras máquinas incubadoras 100 huevos de 58 grs, obtenemos:40 pollitas hembra de 38 grs.
10 huevos claros de 51 grs.
10 huevos no nacidos de 46 grs.
41 machos de 39 grs.
Estas magnitudes las podemos expresar por pollita producida o bien por cada 100.000 pollitas, que es lo podemos nacer habitualmente en nuestra planta de incubación cada día de nacimiento, resultando que por cada 145 grs cargados de huevo incubable por pollita, cada o 14,5 toneladas por 100.000 pollitas, obtenemos:
38 grs de pollitas hembra ó 3,8 toneladas por cada 100.000 pollitas
78 grs de residuo ó 7,8 toneladas que se distribuyen en :
13 grs ó 1,3 ton en huevos claros.
13 grs ó 1,2 ton en cascarones.
12 grs ó 1,3 ton en huevos no nacidos.
40 grs ó 4,0 ton en machitos.
Vapor de agua, pues no olvidemos que la actividad de incubación, es un proceso de secado del huevo incubable hasta un nivel óptimo para obtener una pollita de 1 día totalmente desarrollada.
– Calor, generado en los últimos días del proceso, y que vamos a recuperar para aprovechar en nuestra actividad diaria de incubación.
Como podemos observar en gráfico 1 adjunto, la producción residuos duplica en volumen la producción de masa de pollita de 1 día, lo que hace necesario un análisis pormenorizado para la gestión de cada residuo comenzando por los machitos cuyo peso específico supera más del 50 % de los residuos generados. Obviamente, este ejercicio de gestión va a suponer un ejercicio de valorización y de categorización de residuo a subproducto.
VALORIZACION y PROCESADO DE MACHITOS.
Se trata de un proceso muy consolidado en nuestra actividad, que se lleva a cabo desde hace más de 15 años, en el que hemos conjugado la obtención de una materia prima para alimentar a rapaces, halcones, animales etc ., con el respeto por el bienestar animal.Los machitos son eutanasiados con CO2 tras el proceso de nacimiento e inmediatamente después se someten a un proceso de ultracongelación a -30ºC, con una perfecta circulación de aire, para frenar totalmente cualquier crecimiento microbiano interno. En 24 horas los machitos deben estar totalmente congelados, para posteriormente ser almacenados a -20ºC durante algunas semanas, antes de ser vendidos y distribuidos por todo el mundo.
Estamos ante un claro ejemplo de cómo hacer de la crisis una oportunidad de negocio: sin esta circunstancia, nunca hubiéramos accedido a mercados como puede ser Emiratos Árabes.
VALORIZACION y PROCESADO DE HUEVOS CLAROS y CASCARAS.
prototipo para la gestión de este residuo, que finalmente hemos conseguido valorizar e incluir en diferentes gamas de pienso de porcino, mascotas y avicultura. Los huevos claros son separados mediante miraje automático a los 18 días incubación, en el momento de la transferencia desde máquinas incubadoras a nacedoras. Estos huevos claros descartados para seguir la incubación, son separados por una máquina centrífuga en cáscara y contenido, y de manera automática mediante un sistema de tuberías acceden independientemente a dos silos diferentes a nuestra planta de secado de huevo. Ya en la Planta de Huevo, sometemos al contenido líquido de huevo a un doble proceso: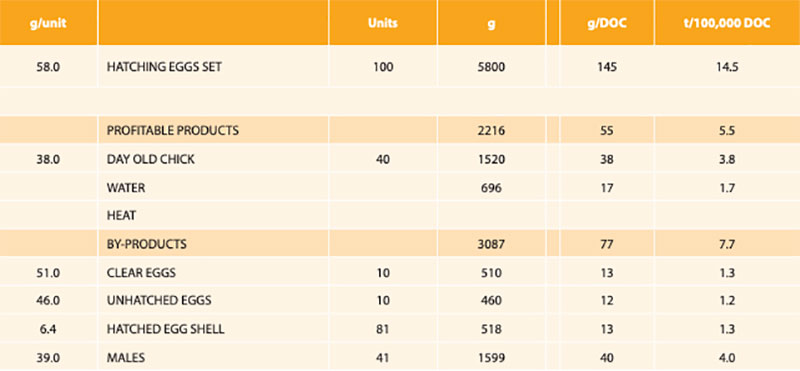
Cuadro 1. Resumen de magnitudes de residuos generados en planta de incubación.
prototipo para la gestión de este residuo, que finalmente hemos conseguido valorizar e incluir en diferentes gamas de pienso de porcino, mascotas y avicultura.
Los huevos claros son separados mediante miraje automático a los 18 días incubación, en el momento de la transferencia desde máquinas incubadoras a nacedoras.
Estos huevos claros descartados para seguir la incubación, son separados por una máquina centrífuga en cáscara y contenido, y de manera automática mediante un sistema de tuberías acceden independientemente a dos silos diferentes a nuestra planta de secado de huevo.
Ya en la Planta de Huevo, sometemos al contenido líquido de huevo a un doble proceso:
1. Coagulación: el huevo durante 20 minutos es sometido a 80ºC para obtener una textura semisólida y poder ser manipulado mejor en fases posteriores. 2. Secado: el huevo coagulado discurre por el interior del secador durante 90 minutos a una temperatura de 245ºC. Como resultado del proceso de secado, obtenemos aproximadamente 11 grs de producto seco por cada huevo claro, resultando una reducción de volumen de casi 5 veces el del residuo inicial.
El producto obtenido, es una excelente materia prima para la alimentación de ganado en general, asegurando los siguientes niveles nutricionales:
Humedad: <12%. Grasa Bruta: >34%. Proteína Bruta: >44 %.
Asimismo, presenta una óptima calidad microbiológica con ausencia de Salmonella y Clostridium, y con Enterobacterias por debajo de 10 UFC En este mismo secador podemos introducir directamente la cáscara, procedente tanto de huevos claros como del nacimiento de pollitos. Esta cáscara es sometida durante 15 minutos a una temperatura de 45ºC para reducir un 30% su peso inicial.
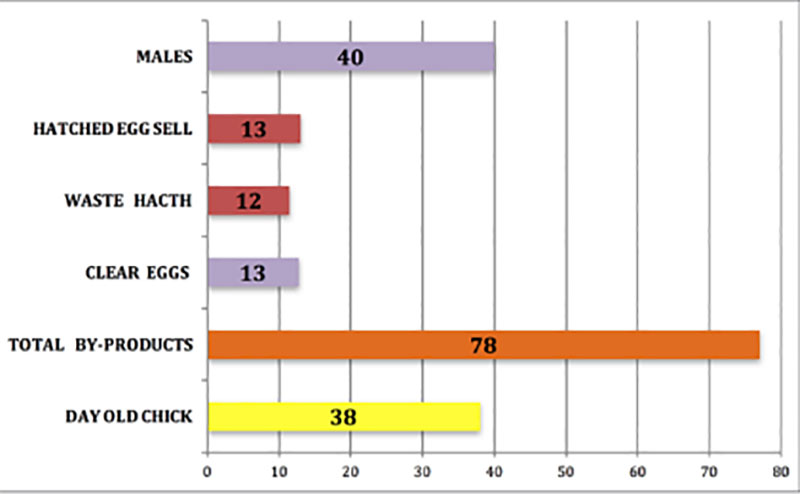
Grafico 1. Producción de Residuos generados por pollita producida( expresado en gramos).
BALANCE COSTE DE VALORIZACION & COSTE DE DESTRUCCION.
La gestión de residuos es ya una línea más de costes en la cuenta de explotación de nuestro actividad, y en su gestión podemos adoptar dos estrategias :Asumir los costes de reciclado a razón
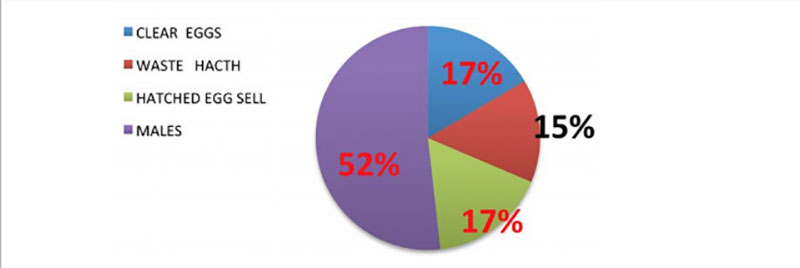
Grafico 2. Distribución de residuos generados (expresados en %).
de 240 euros/toneladas para los restos de nacimiento (Sandach categoría 2 según legislación europea) y a 108 euros/tonelada para resto de residuos (Sandach categoría 3). Lógicamente estos costes dependen de la distancia a las plantas de destrucción, volumen de residuo, producido en cada nacimiento, etc…. Esta gestión de residuos, se cifra en un coste de 1.000 €/100.000 pollitas ó bien en 0,01 €/ pollita producida.
Valorizar los residuos, evitando el coste de reciclado y creando otras líneas de ingresos en nuestra cuenta de explotación. En este sentido, vamos a analizar el tratamiento de cada residuo:
– Machitos. Hemos desarrollado una nueva línea de negocio al margen de la incubación que se ha complementado con otra gama de productos además de los machitos. El resultado económico final, después de costes y amortizaciones, son 480 euros de margen por 100.000 pollitas producidas.
– Huevos Claros. La mayoría de la producción se está incluyendo en la fabricación del pienso para nuestras propias reproductoras y pollitas recriadas de venta, generando un ahorro de 20-30 €/ton en piensos fundamentalmente de primeras edades o de alta concentración de nutrientes.
El resultado económico final de esta actividad es neutro, pero evitamos el coste de reciclado.
Cascaras de huevos claros y de pollitos nacidos. Tenemos la tecnología desarrollada para poder gestionarlo internamente, pero dado el bajo valor del producto final obtenido, es más interesante contratar servicios del gestor autorizado, resultando un costes de 140 €/ 100.000 pollitas.
– Huevos no nacidos en el nacimiento. Es el único residuo que no podemos gestionar en nuestras instalaciones, por lo que tenemos que asumir su coste, por valor 276 €/ 100.000 pollitas.
Recuperación de calor. No nos podíamos olvidar de este punto en nuestro capítulo de reciclado y valorización de los otros outputs generados en el nacimiento. La tecnología actual nos permite recuperar parte del calor producido en el proceso para volver a calentar el agua para las fases iniciales de incubación, así como aprovechar el aire fresco de la noche para ahorrar en el consumo de enfriadoras. Esta iniciativa nos permite ahorrar un 20-25% de gas y electricidad, lo que se traduce en un ahorro de 364 €/100.000 pollitas.
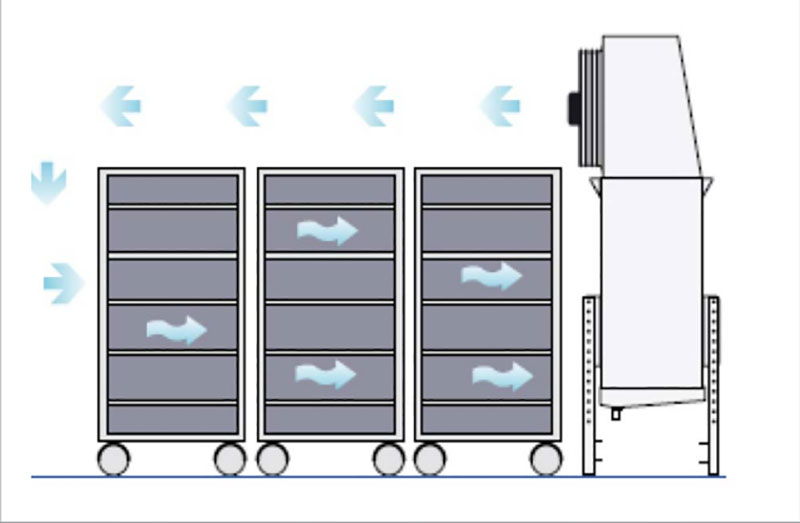
Figure 3. Air circulation inside the deep-freezing tunnel.
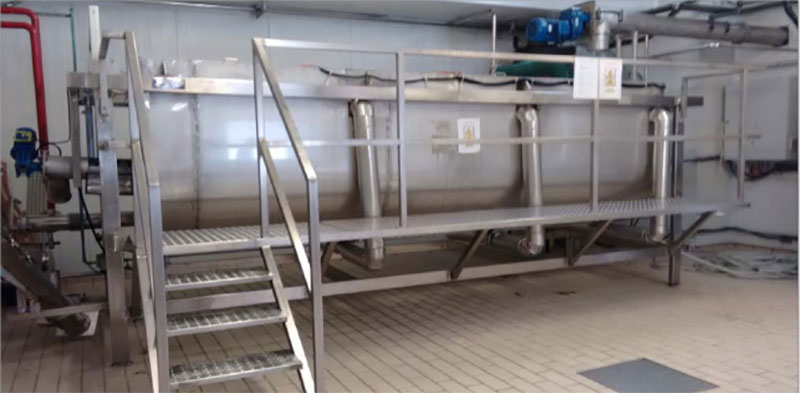
Photo 1. Egg-drying equipment.
Con esta segunda estrategia, estamos gestionando internamente y valorizando el 84-85% de los residuos generados, con un margen de 428 €/100.000 pollitas, lo que supone una ventaja competitiva total sobre la opción de reciclar mediante un tercero de 0,014 €/ pollita producida.
Además de reducir de una manera importante el volumen de residuos (5 veces en algunos casos) y de tener un balance económico positivo en nuestra cuenta de resultados, debemos implementar estas iniciativas en nuestra actividad, pues generan unas mejoras cualitativas que en ocasiones no son demasiado valoradas y/o reconocidas:
– Sensibilización del personal para el cumplimiento de la política de bienestar animal
– Refuerzo para la implantación y mejora de nuestros programas de bioseguridad.
– Compatibilizar nuestra actividad agroindustrial con cualquier otra actividad económica, obligándonos a tener una Planta y Actividad limpia , respetuosa y compatible con el medio ambiente.
Para finalizar, en ocasiones como puede ser ésta, la gestión de algunos problemas o crisis generan situaciones competitivas y oportunidades, tanto en el ámbito puramente financiero, como en el área de mejora de nuestras condiciones de bienestar animal, bioseguridad y compatibilidad de nuestra actividad en cualquier localización.
Pascual Alonso, Ibertec
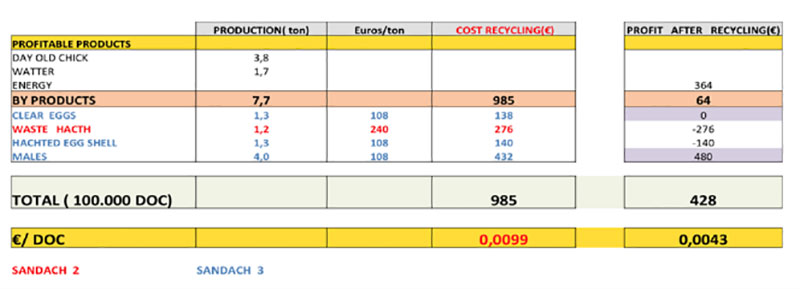
Table 2. Comparison of standard recycling costs and internal recovery by Ibertec.