The management of waste from any livestock operation, and especially hatchery waste, has undoubtedly caused a crisis situation and brought warnings of collapse. This has forced the hatchery sector itself to work diligently to discover the industrial processes that have enabled a large part of this waste to be included in the by-product category, with its associated value. This is how the hatchery sector has transformed a cost and a problem into an income and a business opportunity, and we at IBERTEC have done the same in Spain, at a hatchery producing 15 million LOHMANN chicks a year.
Quantifying waste generation
First, we are going to review the quantities of waste generated in a hatchery. When we load our incubators with 100 eggs at 58 g each, we get:40 female chicks at 38 g each.
10 clear eggs at 51 g each.
10 unhatched eggs at 46 g each.
41 males at 39 g each.
We can express these quantities per female chick, or per 100,000 female chicks, produced. This is the number that we usually hatch in our hatchery per hatch day, so for each 145 g of hatching egg per female chick, or 14.5 t per 100,000 female chicks, we get:
38 g of female chick or 3.8 t per 100,000 females
78 g, or 7.8 t, of waste split between:
13 g or 1.3 t clear eggs.
13 g or 1.3 t egg shells.
12 g or 1.2 t unhatched eggs.
40 g or 4.0 t male chicks.
Water vapour: we must remember that the hatching process dries the hatching egg to its optimum level to produce a fully-developed day-old chick.
Heat: this is generated in the last few days of the process and we recover it for use in our daily hatching operations.
As we can see in Figure 1 above, the weight of waste produced is double the weight of the day-old female chick, so a more detailed analysis of the management of each type of waste is required, starting with the male chicks whose weight exceeds 50% of the total waste produced. This management exercise will obviously require this waste to be recovered and categorised as a by-product.
Male chick processing and recovery
This process has been fully integrated into our operations for more than 15 years, producing a commodity to feed birds of prey, hawks, animals etc., in an animal-welfare friendly manner.Male chicks are euthanised with CO2 after hatching and immediately deep-frozen at -30 °C with optimal air circulation, to arrest any internal microbial growth completely. The males should be completely frozen after 24 hours, and they are then stored at -20 °C for a few weeks, before sale and distribution worldwide. This is a good example of how to make a crisis into a business opportunity: if we had not done this, we would never have gained access to markets such as the United Arab Emirates.
Clear egg and egg shell processing
and recovery Management of the contents of clear eggs was a problem 8–9 years ago so, in collaboration with technology centres and egg-drying equipment suppliers, we decided to create a prototype to handle this type of waste, which we have finally managed to recover and include in various pig, pet and poultry feed ranges. Clear eggs are separated by automatic candling at 18 days’ incubation, when the eggs are transferred from the incubators to the hatchers. These clear eggs, which are rejected from the hatching process, are separated into shell and contents by a centrifuge, and are automatically channelled through a system of tubes to two separate silos in our egg-drying plant. The liquid part of the egg is then subjected to a double process: 1. Coagulation: the egg is heated to 80 °C for 20 minutes, to create a semi-solid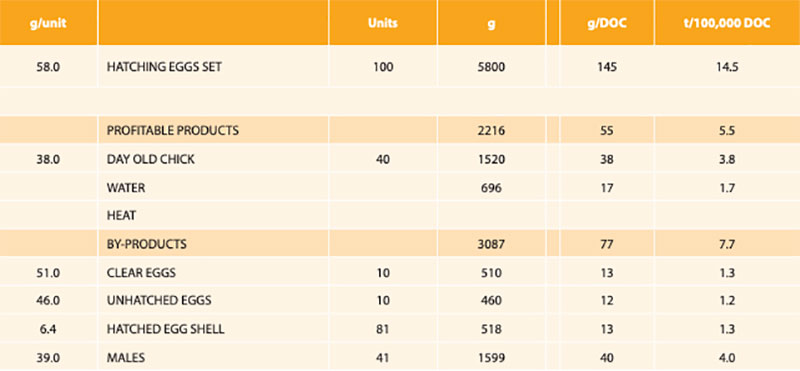
Table 1. Summary of the quantities of waste generated in a hatchery.
texture which can be handled easier in later phases. 2. Drying: the coagulated egg runs through a drier at a temperature of 245 °C for 90 minutes.
Approximately 11 g of dried product is obtained per clear egg as a result of the drying process, reducing the initial volume of waste to a fifth. The resulting product is an excellent raw material for livestock feed in general, with the following guaranteed nutritional value:Moisture: <12%. Crude fat: >34%. Crude protein: >44%.
Microbiological quality is also optimal, with no Salmonella or Clostridium, and with enterobacteria below 10 CFU. The shell from clear and hatched eggs can also be placed directly in this same dryer and subjected to a temperature of 45 °C for 15 minutes to reduce its initial weight by 30%.
The balance of recovery cost and disposal cost
Waste management is now another cost on the balance sheet for our operation, and we can adopt two strategies to manage it:Accept recycling costs of €240/t for hatching waste (category 2 animal by-products not destined for human consumption according to European legislation) and €108/t for the remaining waste (category 3). Logically, these costs depend on the distance to the disposal plant, the volume of waste produced at each hatch, etc. This waste management costs €1,000/100,000 female chicks, or €0.01/female produced.
Recovering waste, avoiding recycling costs and creating other income streams for our balance sheet. We will now analyse the treatment of each kind of waste, from the accounting perspective:
Male chicks. We have developed a new sideline to the hatchery business which is complemented by a whole range of products, as well as the male chicks. The financial end result, after costs and depreciation, is a €480
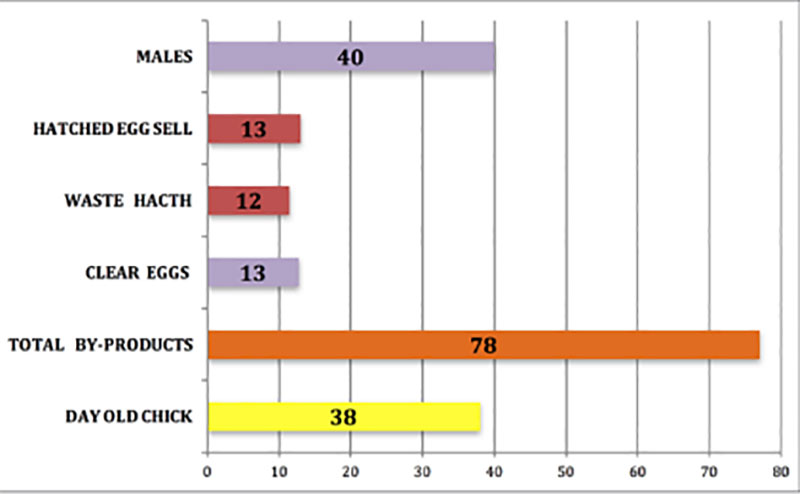
Figure 1. Production of waste per female chick produced (in grams)
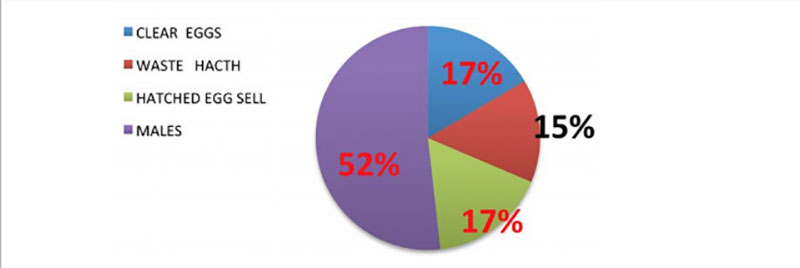
Figure 2. Distribution of waste produced (%)
margin per 100,000 female chicks produced.
Clear eggs. Most of these are used in the manufacture of feed for our own parent stock and point-of-lay birds for sale, generating savings of €23–30/t in feed, mostly early stage or high nutrient concentration rations. The financial end result of this operation is neutral, but we avoid the recycling costs.
Shells from clear and hatched eggs. We have developed the technology to manage these internally but, given the low value of the final product, it makes more sense to contract the services of an authorised company, at a cost of €140/100,000 female chicks.
Unhatched eggs. This is the only waste type that we cannot handle in our facilities, so we have to accept the cost of disposal, at €276/100,000 female chicks. Heat Recovery. At this point in our section on recycling and recovery, we must not forget the outputs generated during hatching. Current technology allows us to recover part of the heat produced during the process, to heat the water for the initial stages of incubation and to make use of the cool temperatures during the
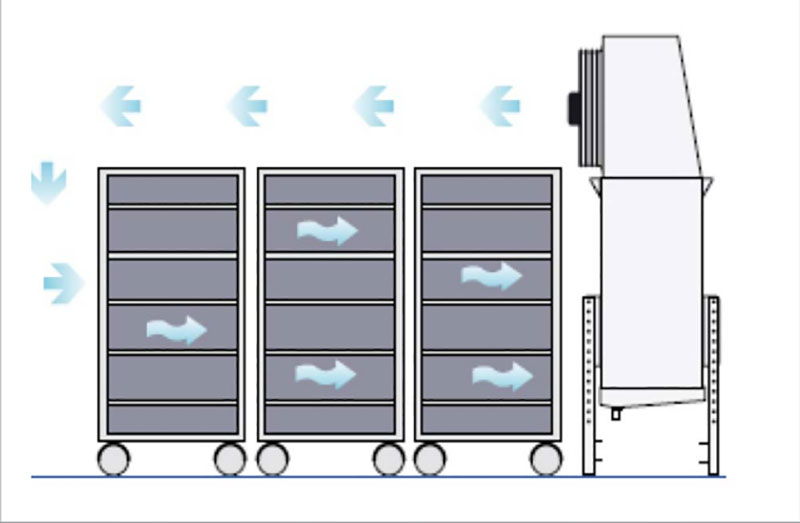
Figure 3. Air circulation inside the deep-freezing tunnel.
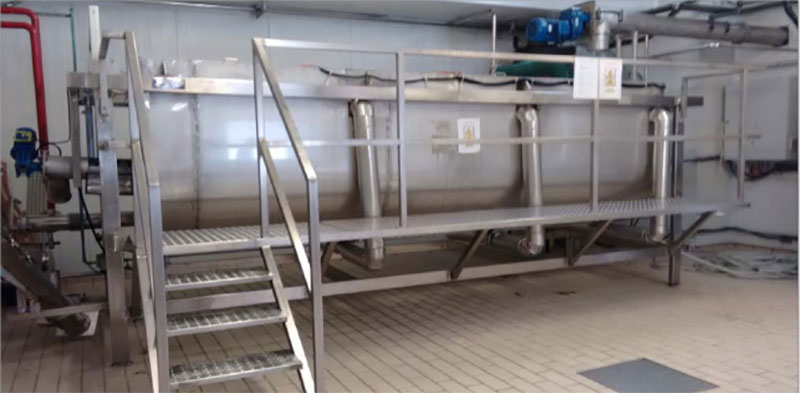
Photo 1. Egg-drying equipment.
night to save on consumption by the coolers. This initiative allows us to save 20–25% of our gas and electricity use, which translates into a saving of €364/100,000 female chicks.
Using this second strategy, we handle and recover 84–85% of our waste internally, with a margin of €428/100,000 females, which is a huge competitive advantage over the alternative of recycling through a third party at €0.014/female chick produced. We must implement these initiatives in our operations, not only because they significantly reduce the volume of waste (five-fold in some cases) and produce a positive financial balance in our profit and loss account, they also generate qualitative improvements that are sometimes undervalued or overlooked.
Staff awareness of the need to comply with the animal welfare policy.
Reinforcing and improving our biosecurity programmes.
Bringing our agro-industrial operations in line with any other economic activity, obliging our plant and operations to be clean, respectful and compatible with the environment.
To sum up, the way that problems or crises are managed in situations such as this generates competitive situations and opportunities. These may be of a purely financial nature, or they might improve our animal welfare and biosecurity conditions, and the suitability of our operations for any location.
Pascual Alonso, Ibertec
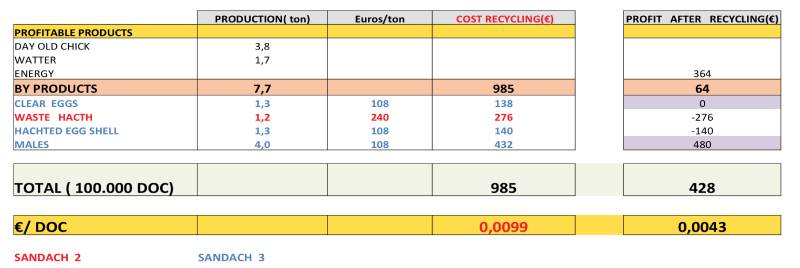
Table 2. Comparison of standard recycling costs and internal recovery by Ibertec.